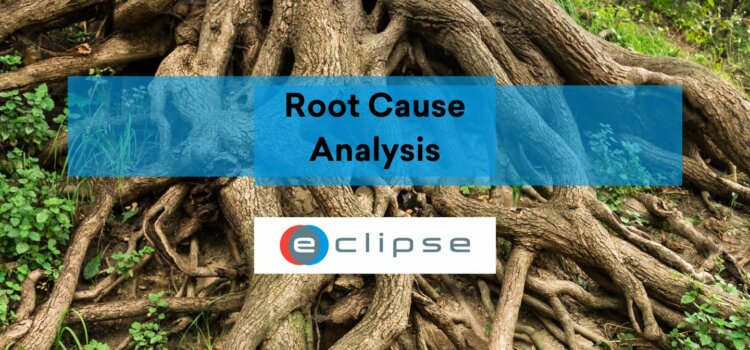
Root Cause Analysis: Meaning, Tools, Pitfalls and More
15 Aug, 2024
A Root Cause Analysis is a problem-solving method to identify the root causes of issues or problems. By identifying and addressing the root causes, organizations can prevent these issues from happening again. This blog post will explore every aspect of Root Cause Analysis. We discuss the meaning, when to use it, who can use it, its goals, different tools, its benefits, its pitfalls, and the software to help you overcome them.
What is Root Cause Analysis?
Root Cause Analysis (RCA) is a systematic approach to identifying the underlying reasons for a problem or failure rather than just addressing its immediate symptoms. The objective is to uncover the fundamental causes that, if resolved, can prevent the issue from recurring.
Consider the example of a car that suddenly stops working. A superficial solution might be to take the bus instead of driving, but this doesn’t address the real problem. To solve the issue, a mechanic would perform a root cause analysis to determine why the car broke downâperhaps discovering that the engine is faulty and needs repair. The root cause is addressed by fixing the engine and preventing the vehicle from stopping from working for the same reason.
RCA in any context involves digging deeper to find the exact cause of a problem and implementing solutions that address that cause directly, leading to more effective and lasting outcomes.
What is the goal of Root Cause analysis?
Root Cause Analysis is primarily implemented to achieve three primary goals. These include the following:
- Identifying the root cause of the problem: Understanding why something occurred in the organization is always the priority when running a Root Cause Analysis. Fixes can become meaningless without specifying why problems happened. Identifying the real issue helps execute appropriate corrective and/or preventive actions.
- Determining the best way to solve the problem: However, identifying the problem is not enough. It is also essential to understand the available solutions. Sometimes, a specific solution is needed to fix an issue, and sometimes, a series of steps is required.
- Drawing conclusions and lessons learned: Understanding what caused the issue and finding the right solution becomes a key to drawing conclusions and learning lessons that help the organization improve.
When should you use a Root Cause Analysis?
RCA can identify the underlying causes of all problems or incidents. Because RCA is typically an intense exercise, it is very useful when problems keep resurfacing despite previous efforts to resolve them. For these issues, it is important to find the reason for the problem that may have been overlooked. After significant incidents, such as major failures or accidents in processes, systems, or products, it is also essential to ensure future incidents are avoided.
RCA is typically being used in projects that have:
- Incident or accident investigation
- Product, project or program quality issues
- System failures
- Process improvement
- Customer complaints
- Regulatory compliance
- Workplace safety
- Environmental incidents
- Operational failures
- Service delivery failures
RCA can even be used proactively in continuous improvement efforts to analyze potential problems before they occur, reducing the likelihood of future issues.
Who can do a Root Cause Analysis?
The organization can employ internal and external teams of experts to investigate the problem. However, this could also depend on the scale of the problem and its impact on the organization. If a major non-issue occurs, a more specialized team of experts has to get involved to analyze the problem broadly. External players could also be involved in executing the Root Cause Analysis to gather findings from an independent perspective, which the organization may badly need to make proper decisions.
What is the typical process of Root Cause Analysis
The process of executing a Root Cause Analysis involves a couple of steps that have to be taken. These include the following:
- Identify the problem: One of the primary goals of a root cause analysis is to identify the problem by gathering all the details that can help explain why non-conformances happened. The root cause is identified and properly documented to help decision-makers in the organization understand the best mechanisms to employ while responding.
- Gather data and document details: The best way to understand the problem is to have as many details as possible. Analyzing and studying the problem ensures every detail is gathered and nothing is left behind. If any detail about the problem is left out, it could seriously limit the organization’s ability to execute effective corrective action in response.
- Solve the problem: When the solution is identified, the next step is to execute an action plan to offset the problem. Corrective actions are usually an organization’s steps to respond to and mitigate the issue.
What are some tools to use during root cause analysis?
There are different types of analysis tools you can use to perform the stages. In this way, Root Cause Analysis is not seen as a fixed process but a goal in itself that can be achieved by using a single tool or various tools and methodologies. The type of analysis used usually depends on the problem being solved and the industry or sector in which an organization operates.
Here are some popular Root Cause Analysis tools:
5 Why Analysis
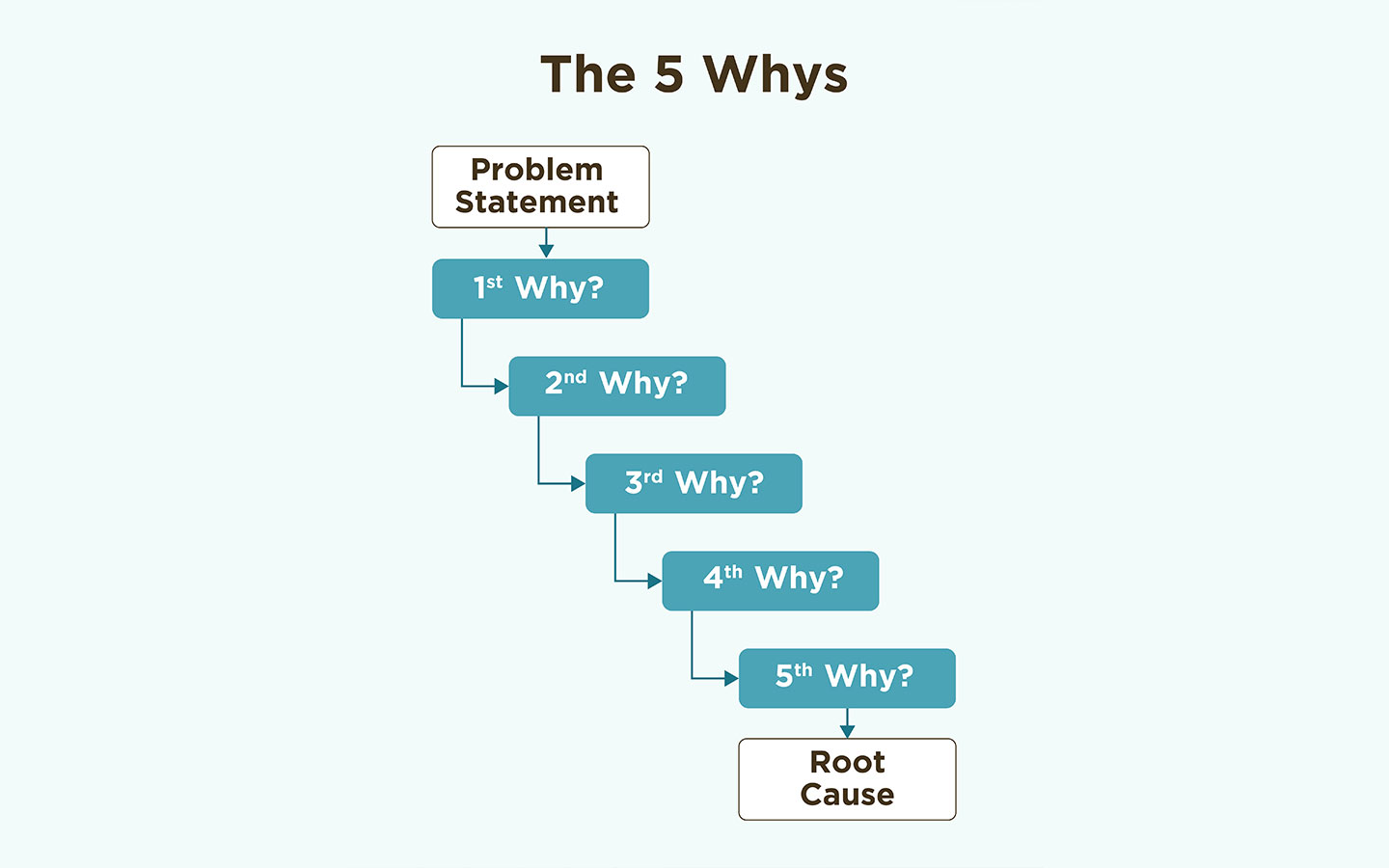
This is a simple yet effective tool for determining the root cause of a problem. As the name suggests, 5 Why Analysis requires problem solvers to ask “why” five times. This helps peel back the layers of a problem until its root cause is uncovered.
The 5 Why Analysis tool is especially useful for simple problems with a linear cause and effect. It’s also quite popular because it’s easy to use and doesn’t require too much data
5 Why Analysis Example
Using the 5 why analysis for a Root Cause Analysis of a broken solar panel might proceed as follows:
- Problem Identification: A solar panel stopped generating power.
- Data Collection: Upon inspection, it was found that the panel’s surface was cracked.
- Cause Identification: Using the “5 Whys” technique:
- Why did the panel stop generating power? Because the surface was cracked.
- Why was the surface cracked? Because a heavy object struck it.
- Why did a heavy object strike it? Because there was strong wind during a storm.
- Why did the strong wind cause damage? Because the panel was not securely fastened.
- Why was it not securely fastened? Because the mounting bolts were not tightened during installation.
- Solution Development: Improve installation protocols to ensure all mounting bolts are properly tightened and use more robust mounting hardware.
- Implementation and Monitoring: Implement the new installation protocols and regularly inspect installed panels for secure mounting.
Ishikawa Diagram
This tool is also popularly used in different industries for Root Cause Analysis. It is also known as a fishbone diagram or cause and effect diagram. The Ishikawa Diagram helps problem solvers visually display the different possible causes of a problem. In this way, it becomes easier to identify the root cause. Steps in using an Ishikawa Diagram include the following:
- Identify the problem.
- Draw an arrow with the problem at the end.
- Draw lines from the arrow with the categories people, machines, materials, methods, environment, and measurements.
After analyzing, you will find the potential causes.
Ishikawa Diagram Example
Using the Ishikawa diagram for a Root Cause Analysis (RCA) of a broken solar panel might proceed as follows:
- Mechanical Failures: physical impact, actuator failure, cracks or fractures, vibration damage
- Electrical Failures: short circuit, open circuit, power supply failure, overheating
- Environmental Factors: space debris impact, temperature extremes, solar radiation, electrostatic discharge
- Human Error: assembly errors, maintenance mistakes, operational errors, launch procedures
- Manufacturing Issues: defective materials, production flaws, quality control failures, contamination
- Design Flaws: inadequate stress testing, poor material choice, insufficient redundancy, design miscalculations
Pareto Chart (The 80/20 Rule)
This is a graphical tool used for prioritization. Pareto Chart is popular and helps organizations identify which areas require immediate attention. The first step in using a Pareto Chart is determining the factors contributing to the problem. Then, these factors are ranked according to their contribution or impact on the issue. After that, a graphical representation is made to see which areas need more attention easily. The Pareto chart is based on the principle that states that 80% of the effects come from 20% of the causes. In other words, a few factors contribute to most of the problems. Fixing this 20% can have a significant impact on the entire system.
Pareto Chart Example
In a Pareto Chart, the causes are listed on the x-axis, while the y-axis represents the frequency or impact of each cause. The causes are typically arranged in descending order of frequency, and a cumulative percentage line is included to help visualize the 80/20 rule.
- Micrometeoroid Impact: 35 occurrences
- Thermal Cycling: 25 occurrences
- Space Debris Collision: 20 occurrences
- Manufacturing Defect: 10 occurrences
- Faulty Installation: 5 occurrences
- Radiation Damage: 3 occurrences
- Power Surges: 2 occurrences
The Benefits of Root Cause Analysis
Root Cause Analysis offers significant benefits to the organization, and these include the following;
Improve decision-making and planning
Any organization must better understand its challenges and how to deal with them. Root Cause Analysis incentivizes the organization’s players to work together and prioritizes better planning. This will help deriving the best mechanisms for solving problems by effectively operationalizing quality management systems in the organization.
Saving current and future costs
Root Cause Analysis provides crucial information about the risks and costs that arise as a result of non-conformance. The organization will be able to understand the costs associated with the problem and how to mitigate them. For example, it could be crucial to understand the following;
- How much has been lost as a result of the issue? This could be the number of revenues or profits an organization lost as a setback after the problem occurred.
- How much will the organization lose if the problem is ignored? When the problem is not effectively handled by ignoring it, it could result in more serious financial losses and other undesirable implications.
- How much does it take to solve the problem? The Root Cause Analysis must include this detail to help decision-makers within the organization who need the right resources to execute the corrective action plan.
Improving efficiency
Root Cause Analysis helps the organization identify and fix issues in its operations. When operational teams do not follow established protocols and procedures, it affects the efficiency and integrity of the entire workflow. Root Cause Analysis can help to;
- Emphasize the need to standardize guidelines. Taking preventative actions based on the findings and investigations will benefit the organization.
- Create a sense of accountability where all players in the organization and the entire business chain live up to standards.
- Engage teams to understand the problems they experience and collect critical information about why issues happen.
Pitfalls of the Root Cause Analysis Process
As much as root cause analysis is essential in quality management, certain pitfalls can make it ineffective. These pitfalls include:
- Relying on common knowledge or assumptions: This usually happens when decision-makers do not want to invest in getting information about the problem. Instead, they want to quickly come up with a solution.
- Not involving all stakeholders: All relevant parties should be at least inspecting the root cause analysis. Failure to do this could result in some ideas not being captured, and as a result, the organization might not be able to resolve the problem.
- Communication: Communicate and report the findings and decisions made to all stakeholders. This ensures everyone is on the same page and working together to solve the problem.
- Not taking action: Sometimes, teams might be reluctant to take action because they still fear the unknown. Next to this, some decision-makers might not want to be held responsible for their actions. Still, it is important to keep moving the project forward, either trust the analysis done and take action, or do another analysis.
- Not tracking problems: In some cases, the Root Cause Analysis might identify a problem that happened in the past, and corrective action is no longer possible. In such a situation, it’s important to have traceability so that similar problems can be prevented.
- Cost involved: Root Cause Analysis, as an entire process, requires resources and a dedicated team to study the problem and document all the required details thoroughly. The analysis needs to contain facts concerning the financial implications caused by the problem.
- Inaccurate data: Corrective actions should be implemented based on evidence. If the organization and its decision-makers rely on inaccurate data, then the interventions they take regarding the identified problem are likely not helpful.
Use eNCTS during your Root Cause Analysis
The eNCTS Module and the ECLIPSE Software Suite help prevent problems by accurately capturing and recording non-conformances, actions, and documents. They ensure all stakeholders have access to the same information and can take corrective action quickly when issues arrive. Contact our experts today to learn more about how you can use eNCTS and the ECLIPSE Software Suite in your organization.
