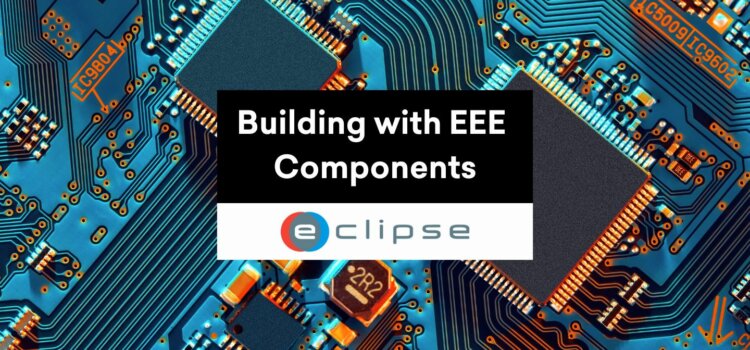
Managing an EEE Database for reliable Space Engineering Components
03 Dec, 2024
The success of any space mission depends on its components. Electrical, Electronic, and Electromechanical (EEE) parts are the foundation of spacecraft, ensuring reliable operation in harsh space conditions. However, managing the lifecycle of these parts is complicated.
Without EEE parts management, space projects can suffer from inefficiencies, delays, and errors. This article explores using EEE programs and databases, common terminology, workflows within EEE programs, and how DAB can help manage EEE databases.
What is an EEE Program?
Typically, EEE programs are specific programs of agencies and large space organizations. EEE programs help to
- Evaluate newly available and advanced electronic components to enhance reliability and efficiency in critical projects.
- Assist organizations in selecting already existing suitable Electrical, Electronic, and Electromechanical components for their specific needs.
- Provide expertise and guidelines for selecting and ensuring parts meet reliability, performance, and safety standards.
- Increase speed through the approval process by outlining what it required to pass approval.
In a broad sense, EEE Parts Programs assist organizations in selecting the most effective Electrical, Electronic, and Electromechanical components for their projects. An EEE program should, therefore, save time and money for the people working with it.
This involves providing information, expertise, and guidelines on the selection process and ensuring that the parts meet reliability, performance, and safety standards. By offering this support, the program helps organizations make informed decisions that align with their projects’ technical and operational requirements.
Security around EEE programs
Access to EEE programs and databases brings their complexities. They are often restricted due to several factors:
- Data sensitivity: Detailed information about components used in critical systems, including proprietary data and specifications that could be sensitive or subject to export control regulations.
- Security concerns: Unrestricted access could pose security risks, as the information might be exploited maliciously.
- Quality assurance: Limiting access ensures that only qualified personnel can make decisions regarding part selection, maintaining proper standards.
- Resource management: Managing and supporting a widely accessible database requires significant resources. Restricting access helps agencies allocate their resources more effectively.
While these restrictions are in place to ensure safety, security, and quality, organizations often collaborate with industry partners. They may provide access to specific information through formal agreements or partnerships.
Common words used within EEE Programs
- DCL (Declared Components List): A comprehensive document listing all the EEE components intended for use or already utilized in a specific payload, platform, or equipment. It ensures traceability, compliance with standards, and consistency across the project lifecycle.
- PAD (Parts Approval Document): A formal document submitted to request approval for a specific component to be used in a project. It includes detailed technical specifications, qualification status, and ECSS or mission-specific standards compliance.
- Qualification Testing: A series of tests conducted to verify that a component meets the required standards for space use, including radiation resistance
- FMEA (Failure Mode and Effects Analysis): A systematic process used to identify potential failure modes of components and their impacts on the system, ensuring risks are mitigated early in the project lifecycle.
- RFD (Request for Deviation): A formal request to use a component that does not fully meet project specifications but is deemed acceptable under specific conditions.
- RFW (Request for Waiver): Similar to an RFD but used when a standard or requirement is not applicable or must be waived for practical reasons.
- NRB (Non-Conformance Review Board): A team or panel responsible for evaluating and resolving issues related to non-conformances in components, such as manufacturing defects or performance deviations.
What is an EEE Database?
Now that we’ve explored EEE programs, let’s look at EEE databases. An EEE database (Electrical, Electronic, and Electromechanical) is a specialized system for storing, managing, and retrieving engineering data related to components, devices, and systems critical to various industries, particularly the space sector. These components are categorized as follows:
Electrical components use electricity for power distribution and control. They include:
- Wires for transmitting electrical current.
- Switches for enabling or disabling circuits.
- Power circuits are used to manage and distribute electrical energy to ensure functionality.
Electronic components manipulate electrical signals to process information, control systems, or execute specific tasks. Examples include:
- Microchips and semiconductors for computational and signal processing functions.
- Resistors and capacitors are used to manage current flow and store energy.
Electromechanical components combine electrical and mechanical systems, often converting one form of energy into another. Key examples are:
- Motors and actuators are used to convert electrical energy into motion.
- Relays for switching circuits using electromagnetic principles.
Next to these components, some databases will also contain:
- Research paper, design, and technical specifications.
- Requirements and standards.
The goal should always be to make an EEE database user-centric and intuitive so that engineers, project managers, and other stakeholders can easily access, update, and analyze critical component data.
Examples of EEE databases
NASA’s Parts Selection List (NPSL) is designed as a tool for NASA-affiliated organizations. It provides a curated list of EEE parts that meet specific quality and reliability criteria. Similarly, ESA has its qualification programs and databases for EEE components tailored to its projects, mission requirements, and standards, including the European Space Components Information Exchange System (ESCIES).
Databases and EEE Databases
One might ask, what is the difference between a normal component database and an EEE database? The answer lies in looking at the details and users. EEE databases are used to manage detailed information about space-grade components. These databases focus on the technical specifications, reliability metrics, lifecycle status, radiation tolerance, and qualification records of components critical for mission hardware. Their primary purpose is to assist engineers and procurement teams in selecting components that meet the stringent requirements of space missions, ensuring reliability and compliance with international standards.
In contrast, normal space databases are broader in scope and cater to space organizations’ overall data management needs. These databases store custom mission data, results, approval cycles, reviews, risk documents, and non-conformance management documents. They are primarily used by a wider group of scientists, mission planners, program managers, documentalists, and space engineers to support mission planning, execution, and operational management.
How are different teams using the EEE database?
- Collaboration within the space industry: The EEE database facilitates industry-wide collaboration, allowing multiple organizations, including agencies, contractors, and manufacturers, to share and harmonize component data.
- Risk mitigation and compliance: Organizations use the EEE database to track component performance under extreme conditions, such as radiation and temperature, ensuring compliance with both industry standards and mission-specific requirements.
- Knowledge retention and training: The EEE database is a centralized repository of validated data, supporting knowledge transfer and training for engineers, project teams, and procurement specialists within the space sector.
- Custom mission planning: Agencies and private companies rely on the EEE database to select components tailored to unique mission parameters, guaranteeing compatibility and reliability in specific environmental conditions.
- Specify requirements for space components: Standards like ECSS-Q-ST-60C Rev.3 guide the management of the EEE database, ensuring components meet strict performance, reliability, and qualification criteria for space missions.
Additional uses of the EEE database
- Streamlining procurement processes: The database enables detailed tracking of the entire procurement cycle, from quotation to delivery, ensuring that components meet cost, timeline, and technical specifications.
- Component lifecycle management: Teams use the database to monitor the lifecycle of parts, including testing, qualification, and reusability for future missions, improving long-term project efficiency.
- Pre-qualified parts access: The database allows teams to access lists of pre-qualified components, reducing time spent on qualification and improving reliability in subsystem designs.
- DCL creation and approval: Organizations utilize the database to build, review, and approve Declared Components Lists (DCLs) with traceable workflows, ensuring accuracy and compliance across all stakeholders.
- Standardization: Standardization is important within the space industry. By aligning with ECSS, for example, and leveraging input from ESCC members, the database supports standardization across international space projects, simplifying cross-border collaboration.
- Innovation and knowledge sharing: Integrating tools and initiatives from groups like NEPAG and ESCC enhances the database’s utility for sharing best practices, qualification results, and industry trends.
- Enhanced decision-making: Teams utilize historical data from the database to evaluate the performance of components in previous missions, enabling informed decisions for new projects.
- Cost-risk balancing: The database can help classify components to align mission-critical needs with cost constraints.
The EEE database remains vital for enabling efficient, compliant, and collaborative workflows across the global space industry.
Managing your EEE Database with DAB
DAB, short for Database Application Builder, is a flexible module for creating bespoke databases and workflows. Unlike off-the-shelf solutions, DAB allows you to design a system from scratch, ensuring it aligns perfectly with your project requirements.
Customizing your EEE database
To manage space-qualified components effectively, your database needs to capture critical information, such as:
- Component type and specifications
- Manufacturer and distributor details
- Space qualification status
- Associated documentation, including test reports and approval records
You can design a database using DAB that tracks all these details. The interface allows you to define fields, categories, and relationships between data points, creating a system that stores information and makes it easy to retrieve and analyze.
Procurement of parts
Procurement of EEE components involves far more than simply purchasing parts; a range of activities is also involved. Key areas of expertise in the procurement process include:
- Market survey: Identify reliable suppliers and assess the availability of components that meet project requirements.
- Component selection: Evaluating and choosing components based on technical specifications, compliance, and mission needs.
- Make-or-buy decisions: Determining whether to manufacture components in-house or procure them from external suppliers, considering cost, capability, and timelines.
- Definition of procurement specifications: Establishing detailed requirements for components, including performance, quality, and environmental tolerances.
- Planning and cost control/budgeting: Managing budgets and ensuring cost efficiency throughout the procurement lifecycle.
- Stock Control: Monitoring inventory to maintain optimal stock levels and avoid shortages or overstocking during the project lifecycle.
Workflows within EEE programs
Managing EEE parts isn’t just about storing data; it’s about managing the lifecycle of each component. With DAB, you can create workflows to handle key processes, such as:
- Approval workflows: Route components through structured review and approval steps to ensure they meet project requirements.
- Classification workflows: Organize parts by type, project, or qualification status for easy access.
- Deviation and waiver workflows: Handle exceptions efficiently while maintaining a clear audit trail.
These workflows are fully customizable, enabling your team to work in a way that matches your existing processes while improving overall efficiency.
Example workflow when using an EEE Database
One of the core workflows involves Qualification, Selection, and Collaboration, which focuses on identifying the right components for specific mission needs and ensuring their compliance with project standards.
- Identify mission requirements
- Search the database for pre-qualified components
- Share parts data with stakeholders for review and feedback
- Add selected parts to a project-specific Declared Components List (DCL)
- Submit the DCL for approval, incorporating any necessary updates from the collaboration
DAB for EEE Management
DAB offers several advantages over traditional tools like spreadsheets or generic databases:
- Flexibility and customization: Unlike pre-packaged solutions, DAB allows you to build a database tailored to your needs. This ensures the system works for you rather than forcing you to adapt to its limitations.
- Improved efficiency: Automated workflows reduce the time spent on administrative tasks, such as approvals and document management. Team members can access the latest information with real-time updates, minimizing delays and miscommunications.
- Enhanced collaboration: DAB’s role-based access controls ensure people can access the right data. This fosters better collaboration across teams and organizations, as everyone works from a single source of truth.
- Security and compliance: security management is more essential than ever. DAB addresses this with robust access controls, version history, and audit trails, ensuring compliance with industry standards and aligning with best practices for EEE parts assurance.
Going beyond EEE Parts with DAB
While DAB is an excellent tool for managing EEE parts, its capabilities extend beyond this use case. Organizations can use DAB to build databases for a variety of purposes, such as:
- Lessons learned: Capture and share insights from past projects.
- Project milestones: Track key financial and engineering events.
- Requests for deviation or waiver: Handle large-scale changes securely and efficiently.
By consolidating multiple workflows and databases within a single platform, DAB helps organizations achieve a cohesive data management strategy.
Conclusion
The Database Application Builder (DAB) from the ECLIPSE Software Suite provides the tools to build a custom database and workflows that streamline this process from beginning to end.
By replacing spreadsheets with a centralized, secure, and adaptable system, you can improve efficiency, enhance collaboration, and ensure compliance with industry standards. And because DAB is designed for flexibility, its benefits extend beyond EEE databases, supporting a wide range of other data management processes.
Start building with DAB today if you’re ready to take control of your data and transform how your team works. The future of EEE parts management lies in smart, customized solutions that align with the demands of modern space engineering.