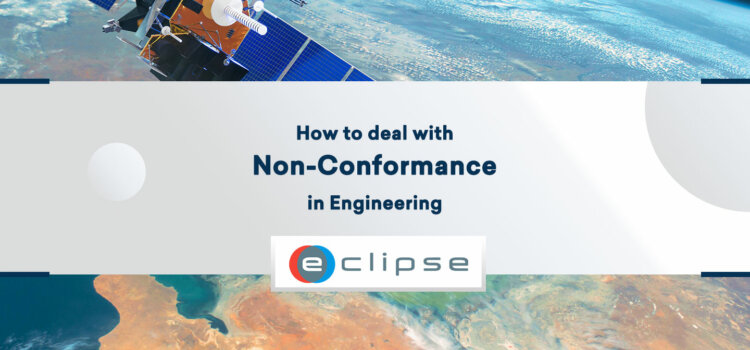
Non-Conformance: Types, Preventing, Identification, and Handling
01 Apr, 2025
Non-conformance (NC) occurs when a product, service, process, or business operation fails to meet requirements. These requirements may be set by external organizations or specific to the organization itself.
Requirements are often set to meet specific standards to avoid risks, failure, and costs. When an organization’s operation fails to meet a requirement, this is called a Non-Conformance.
Different words, same meaning
Not every company uses the same term non-conformances. You might hear non-compliance, deviation, anomaly, or non-conformity instead. While the words vary, they all describe the same issue: a mismatch between what was required and what actually happened.
A common example
Imagine a company that designs a product with specific measurements and features. If the final product doesn’t match those specs, that’s non-conformance. It signals that the process didn’t deliver what was promised, and corrective steps are needed.
Why a Non-Conformance matters?
Failure to meet and follow requirements such as specifications, standards, and guidelines could result in delivering a bad product. Non-conformance can also increase serious risks and liabilities for the organization, as it could manifest in product errors, misconfigurations, and malfunctions and affect end-user experience.
Types of Non-Conformances
Non-conformances are often categorized as minor or major, though other classifications exist depending on the industry.
Minor Non-Conformance
Minor Non-Conformance occurs relatively small and doesn’t impact the entire organization. So, this type of Non-Conformance leads to limited consequences and is easier to solve. For example, minor alterations to product documentation could be considered minor conformance. This could be quickly fixed by updating the relevant documentation.
Minor non-conformances may seem small, but they should be addressed quickly to prevent escalation. If left unchecked, minor Non-Conformances can snowball into major ones. Therefore, organizations need to have systems and processes in place to identify and correct minor Non-Conformances before they turn into major ones.
Major Non-Conformance
A major Non-Conformance broadly affects the entire production or workflow of the organization. The problems that arise from major Non-Conformance can have a far-reaching impact on the final product. An example of major Non-Conformance includes supplying untested products or making unofficial and unendorsed changes to the production and failing to document and follow up on the changes.
A major Non-Conformance can have a huge impact on the reputation and branding of an organization or business. Sometimes they are costly to fix and usually require more effort, time, and resources to be corrected compared to a minor non-conformance. Therefore, it’s important for businesses to have systems and processes in place that can help to identify and correct major Non-Conformances before they cause any serious damage.
Want to make Non-Conformance Management easier, faster, and more structured?
Use the ECLIPSE Software Suite
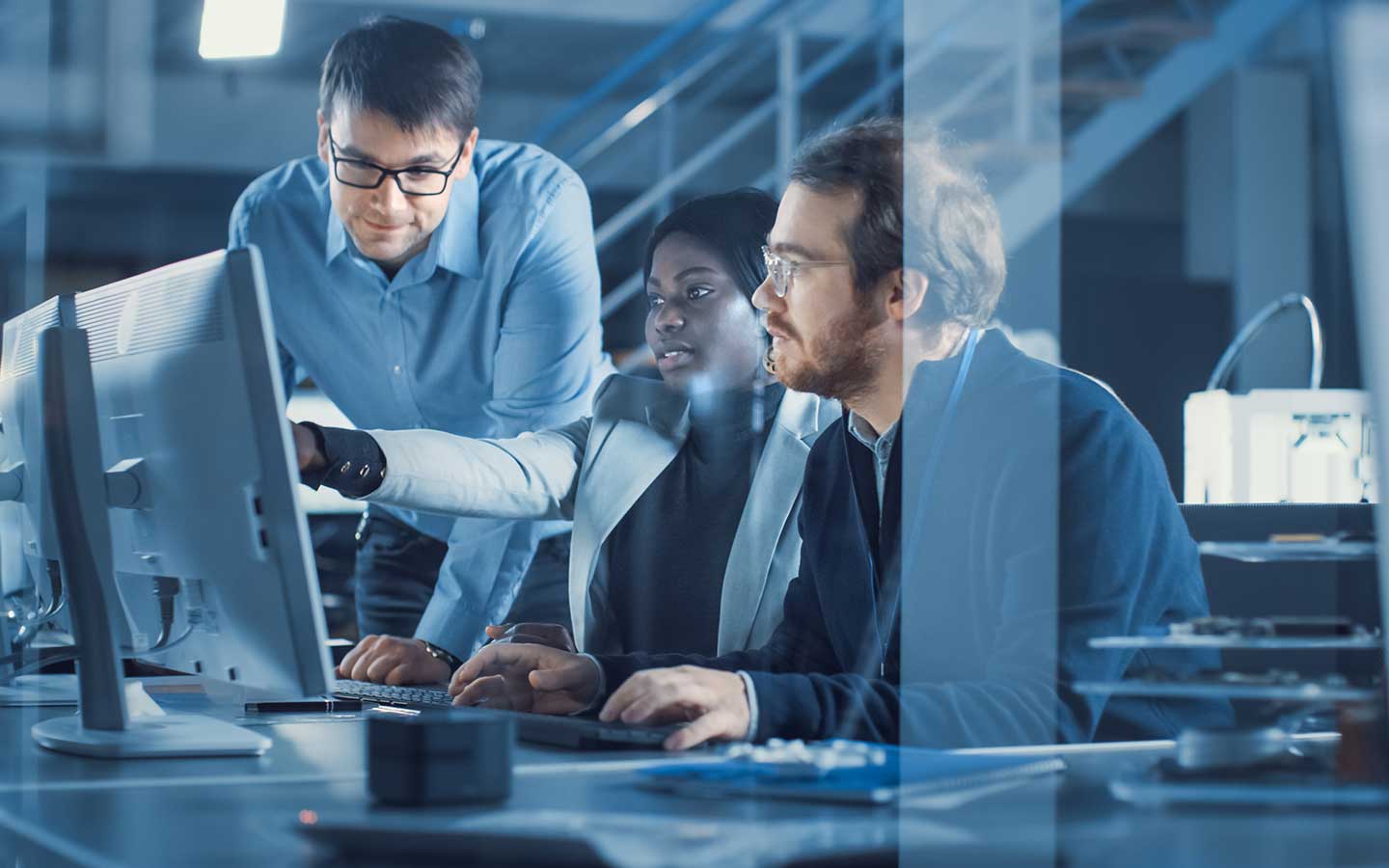
Tips to prevent Non-Conformance
As the popular saying goes: “prevention is better than cure”, it’s important to establish proper procedures and critical measures aimed to curtail Non-Conformance before it happens. There are several steps to take in order to achieve this:
Perform risk analysis: This is the first and most important step to take in order to prevent non-conformance. By performing a risk analysis, businesses can identify potential risks that could lead to non-conformance. Once these risks are identified, businesses can put in place measures to mitigate or eliminate them. Managing your risks can be done with eRISK, a module of the ECLIPSE Software Suite.
Design and adopt a framework for Quality Management System (QMS). Under this framework, product design, quality assessment and proper auditing are standardized and strictly adhered to throughout the product manufacturing process and up to when that product reaches the end-user.
Train employees on the following Standard Operating Procedures (SOP): Company employees may need proper training to equip them with the necessary knowledge and skills about the defined procedures, requirements and specifications that have to be achieved in the workflow
Testing and iterative testing: Before the product is moved to the final stage of delivery to the end-user, Testing and iterative testing procedures should be implemented to avoid misconfigurations, improper documentation, and other mistakes that could manifest before it’s rolled out on the market.
Communication standards: There should be a well-defined communication channel between workers on the floor, managers, and executives. This will ensure that everyone is kept in the loop about updates, changes, and requirements that have to be met in order to avoid Non-Conformance.
Document security: There should be a clear and well-defined procedure for handling, storing, and retrieving documents. This will help to reduce the chances of mix-ups, misplaced documents, and incorrect versions being used during the manufacturing process. A document management system can be very helpful in this regard.
Assess suppliers, partners, and contractors: Suppliers, partners, and contractors play an important role in ensuring the quality of the product. Therefore, it’s important to carefully assess and select suppliers with a good track record of providing quality products and services. Next to this, they will need to have systems and processes in place to report, prevent and correct any Non-Conformances that may occur and should be able to communicate effectively with their clients.
Accountability through traceability: Whenever there is an error. Registry, analysis and intervention are needed. Identifying what happened and the reasons why it happened is essential for this: in short traceability is necessary. To achieve this, organizations need to put in place systems that can help track and trace documents, actions, risks, non-conformances, and other database items.
Identifying Non-Conformance
Information and insights are valuable because they help organizations identify Non-Conformances and respond with appropriate corrective action. There are several ways an organization can identify Non-Conformances, these include:
Monitoring and review
There should be a mechanism in place to monitor and review the design, manufacturing, delivery, and in-operation phases. This helps to identify any areas of improvement and make the necessary changes to prevent Non-Conformance.
Using internal reviews
Every organization has to evaluate itself, assess its business processes and also examine important feedbacks that require thorough attention. This kind of arrangement helps the organization reinvent itself to adopt proper systems and processes designed to prevent Non-Conformance from happening.
Using both internal and external auditors
The organization can have its own Quality Assurance Management framework with a team of its own experts overseeing the entire process. But to further build confidence within the entire ecosystem, external quality inspection and audit could be involved to study the organization’s QMS framework and its implementation.
Understanding Key Performance Indicators (KPI’s)
Performance indicators could be a checklist of procedures that must be met throughout the entire workflow of the organization. When any of these procedures are not met or when deviations are identified. This could indicate a Non-Conformance.
Customer complaints and customer feedback
Customer feedbacks offer an insight to understand if a given product provides the actual quality as expected. Poor customer feedback could be a serious signal that something wrong could have happened somewhere either during the manufacturing procedure or during product shipment and handling.
Want to make Non-Conformance Management easier, faster, and more structured?
Use the ECLIPSE Software Suite

Dealing with Non-Conformances
Simply put, once Non-Conformance has been identified, the Non-Conformance needs to be corrected and the process or product improved to prevent escalation and reoccurrence. In other words, the Non-Conformance needs to be fixed.
There are several tasks an organization can do when dealing with an identified Non-Conformance they are:
Understand the cause of the problem
The organization’s internal QMS Audit team are tasked to evaluate all the established procedures and processes and understand how effective they’re. They study the problems and understand what could be causing them. For example, if the problems are caused because of deviation from following the required manufacturing procedure then, this could be noted and taken into consideration.
The organization team can further choose to escalate its investigations into its processes to deeply and broadly understand the issue. The evaluation process can be necessary as it helps to identify all problems and gives the organization the right picture of what type of corrective action is needed to solve the problem at hand.
There are several tools you can use to do a root cause analysis such as the 5 Why’s Analysis, Ishikawa Diagram (fishbone diagram), and the Pareto Principle.
Create a Non-Conformance Report
After the process of identifying the problem, there is a need to properly document the findings associated with Non-Conformance. This documentation can serve as the study and analysis report which helps key decision-makers to understand the gravity of the situation so they can take the required action. Documenting Non-Conformance involves writing a Non-Conformance Report (NCR) and typically you have a standard content arrangement and standard formatting you will follow when writing it.
Segregating non-conforming products
If it’s discovered that a couple of products don’t meet the desired standards, then the organization can decide to separate them for further evaluation and study. At this point, such products are prevented from entering the market as they could be regarded as unfit for the customers. Segregating non-conforming products ensures they donât reach customers and allows time for evaluation and correction.
One of the other reasons why segregating is needed is to help understand the best way to rectify the problem. Non-conforming products should be taken seriously, as trying to compromise may lead to undesirable consequences that could affect the organization’s entire operations.
Fixing the Non-Conformance
After taking the actions aforementioned, it’s now time to work on fixing the identified problem by implementing corrective and preventive action. The aim is to fix the problem in such a way that it will not reoccur in future and if possible improve the product or process so that it meets or even exceed the standard quality requirements.
The tasks above are typically executed within the steps of a Non-Conformance Process. This process is a part of the organization’s larger quality management system.
A word from ECLIPSE Suite
Non-Conformance is inevitable in any organization but with the right quality management system in place, you can properly deal with it when it happens. With the ECLIPSE Suite, you have a complete tool that helps you take care of all your quality management needs including Non-Conformance management. Create custom and compliant Non-Conformance Reports with eNCTS, learn more and contact our team today.
